Microelectronics
Highest Purity for contamination-free Chip Production
From Sand to Chip. With Safety.
The demand for ever more, ever more compact and ever more powerful microchips is growing continuously. This also increases the demands on process conditions and air purity. The production of microchips and other electronic components is technically complex and extremely cost-intensive. To minimize the costs per component, it is important to optimally coordinate all individual processes and minimize the reject rate. Pure and high-purity process conditions make a decisive contribution to this. As one of the innovation and quality leaders in the field of contamination control and cleanroom technology, we offer proven components and economical comprehensive solutions.
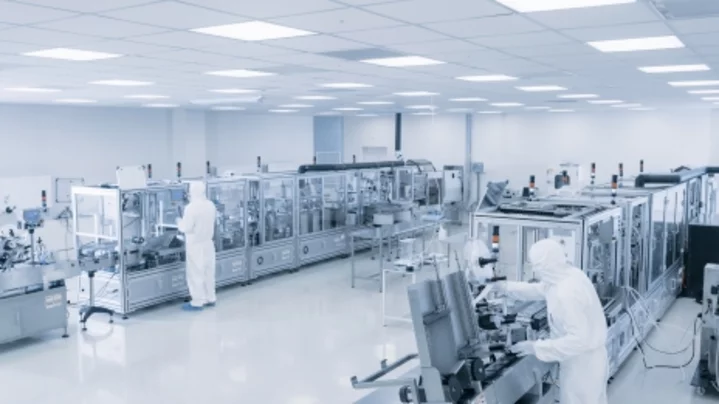
Specific Requirements
Semiconductor production takes place in several hundred manufacturing steps, starting with the frontend (including lithography, etching, coating) through to the backend and packaging. These take place under cleanroom conditions continuously, but require different cleanroom classes. To ensure that the electrical circuits are operating permanently without trouble, attention must be paid to compliance with the required cleanliness and process conditions right from the production of the high-purity silicon wafers and the necessary process chemicals. This reliably protects production from airborne particles and molecular contamination. Depending on the process step and requirements, cleanroom conditions from cleanroom class ISO 8 to ISO 1 are needed.
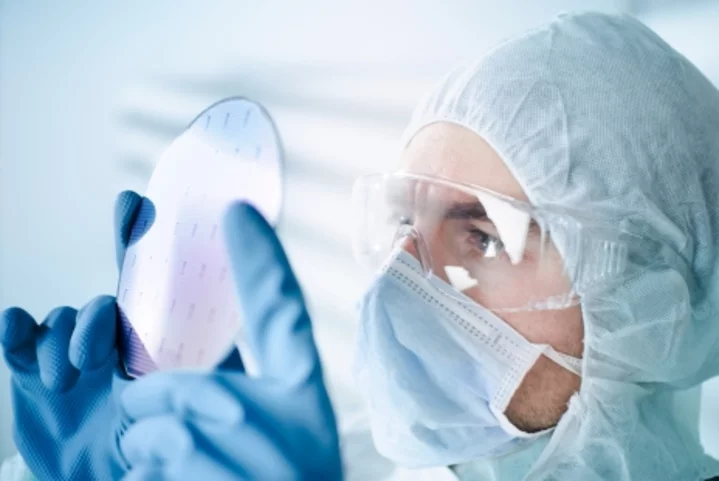
Solutions
Our comprehensive portfolio offers future-proof solutions and components for almost all process steps and manufacturing requirements. If required, we develop customized solutions for special requirements and special processes.
Cleanrooms: Our turnkey cleanroom solutions up to cleanroom class ISO 5 and better ensure particularly clean, low-particle air conditions and exactly the climatic conditions you need for chip manufacturing.
Measuring Rooms: Our turnkey measuring rooms create extremely constant and precisely defined measuring conditions for chip production. All parameters such as temperature and air humidity can be controlled and regulated to the process-oriented.
Process Climate Systems: Our system solutions for the process climate ensure anytime that all climate conditions are constantly and most precisely met and that your processes can be optimally run.
Customized Solutions: We also plan and implement all other individual clean room and air conditioning solutions for you, professionally and according to your demands, from a single source.
Oven systems for semiconductor production
The process of manufacturing semiconductors and electronic components involves numerous steps and usually has very specific requirements in terms of process conditions. To ensure that these can be produced reliably every time, perfectly coordinated technology is required. The industrial vötschovens from Weiss Technik help to create these conditions in the front and back end in a way that is repeatable, safe and economical.
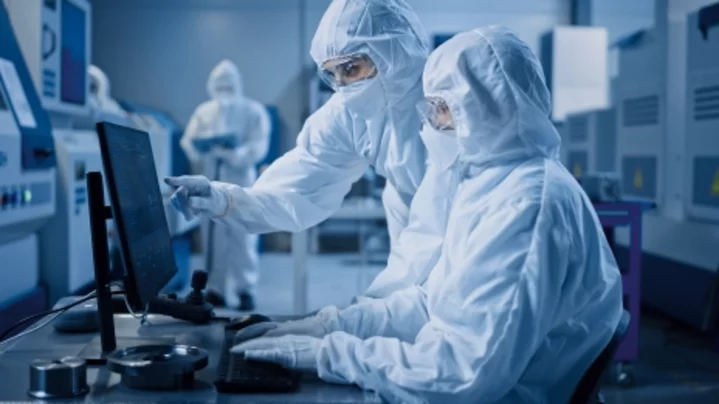
Our Services
With our flexible service modules, you benefit from our comprehensive know-how. Whenever you need it, and always exactly as you need it: In individual project steps, with components or with us as general contractor.
- Consulting and Planning
- Construction and Execution
- Agile Project Management
- Installation Service and Commissioning
- International After-Sales Service
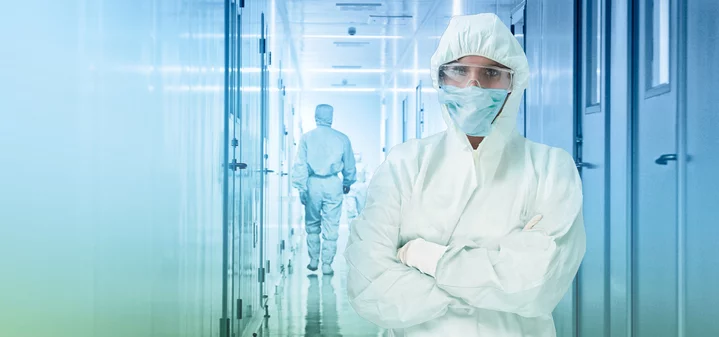
Our Products
We use our high-quality components to equip areas with special climate requirements. These include, for example, research laboratories and parts of chip production halls. In addition to basic components, we also offer customized solutions:
- Filter Fan Units (FFUs)
- Workbenches and laminar flow units
- Mini-Environments
- Air-Conditioning and Refrigeration
- Adsorption Dryers
- Cleanroom Cabins
- Wall, Ceiling and Floor Systems, Lighting and Media Supply
- Personnel and Material Locks
- Monitoring Systems