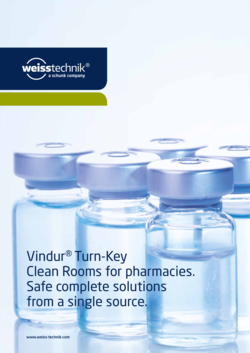
Vindur® Turnkey Clean Rooms for pharmacies
Industry brochure
Pharmacists who want to produce cytostatic drugs, parenterals and other sterile medicinal products need a qualified and validated clean room. The planning, implementation and official approval of this involves considerable effort: in terms of time, finances and organisation. Weiss Technik provides pharmacists with holistic support, from needs analysis and process planning to execution, commissioning and qualification/requalification.
For cleanrooms in pharmacies and laboratories. Pharmacies and hospital pharmacies as well as compounding centres are subject to numerous regulations and guidelines, just like manufacturers of pharmaceutical products. That is why the forward-looking planning and conscientious realisation of cleanrooms require comprehensive specialist knowledge.
The preparation and production of parenteral nutrition, cytostatic drugs and other medical products such as CMR substances (carcinogenic, mutagenic or toxic to reproduction) as well as for packaging as blister solutions. Also other sterile preparations such as ophthalmics, antibiotics and pain cassettes as well as parenteral mixed infusions.
Cleanrooms in pharmacies are subject to strict regulations to ensure the safety of products and customers. Our cleanroom solutions fulfil all important standards and guidelines:
As experienced specialists in cleanroom technology, we have been serving pharmacies and pharmaceutical production facilities as well as laboratories for many years. We know the legal requirements, the practical demands and also the economic aspects very well. Which means we can classify and incorporate these three criteria and implement them in line with requirements and processes.
Our range includes systems for complete cleanrooms as well as components: functional and comfortable cleanroom cabins, class 2 safety workbenches, laminar flow cabinets and isolators. The scope of services ranges from the room concept to the technology to monitoring and beyond. We accompany the entire project from the planning phase through to day-to-day practice: with consultation, planning, qualification, implementation and after-sales service.
The first important planning factor is the spatial conditions on site. Taking the desired production capacities and the product portfolio into account, we develop a concept for the future standard-compliant laboratory or cleanroom area together with our customers. First of all, a room layout is drawn up. This covers the areas of personnel and material locks, preparation, mixing and production. In compliance with the cleanliness classes and pressure levels, these are coordinated with the personnel and material flow. Subsequently, the locations for safety workbenches, laminar flow systems or isolators, airlocks and laboratory furniture and equipment, for example, are determined.
We look at the whole space – floor, walls and ceilings – and pay attention to all the important details for you. These include, for example, enclosure surfaces in accordance with the EU GMP guidelines, which must be easy to clean, possible to disinfect, smooth and free of cracks. We deliberately plan the accessibility of the supply technology outside the clean zones. The advantage of this is that checks, maintenance and repairs can be carried out in some cases without suspending the cleanroom status.
Intelligent ventilation technology
Cleanroom-compatible ventilation is a question of technology. In addition to safe and effective operation, our air-conditioning units and ventilation technology also offer a system that is optimally matched to the overall system concept in terms of energy. You save energy and costs.
The automated, patient-specific blistering of medicines is increasingly gaining acceptance for good reasons: automated processes save time and costs, prescriptions can be better controlled and the supply of medicines becomes safer. Last but not least, the blistering service strengthens the confidence of the patients and nursing homes to be supplied, and thus promotes customer loyalty at the same time. The guidelines for cleanrooms for the blistering of medicines correspond to those for the production of solid dosage forms. They apply just as much to manufacturing operations as to patient-specific pharmacy operations. We implement these strict requirements within the framework of the entire room concept in accordance with applicable regulations without exception. We advise and accompany you throughout the entire project and offer you turnkey solutions.
In our planning and realisation, we pay particular attention to the areas of deblistering and blistering, but also to the area of quality control as well as storage and dispatch of the finished blisters. In order to comply with the cleanroom requirements for handling open products, it is essential to have smooth, easy-to-clean and disinfect walls. In addition, a pressure level concept and suitable personnel and material locks must be provided.
The cleanroom requirements:
Industry brochure
Case Study
With our new contact filter, you can find the right contact person for your request in no time—quickly, specifically, and personally.
Simply filter, select a contact, and get started right away!
There are no contacts available. Please make a selection.